J’ai passé beaucoup de temps récemment à m’initier aux machines-outils à commande numérique (CNC). Apprendre à m’en servir, en construire, apprendre à en construire. Cet article est une introduction à ces défis, à leur nécessité, à l’étendue de ce que les procédés de fabrication en CNC permettent.
Au sommaire :
Pertinence et usages des CNC
Mes choix de matériels, construction et logiciels
Compétences requises
Mes projets de CNC à court et long terme
Pertinence et usages des CNC
S’il est possible réaliser des véhicules par la seule dextérité de ses mains, il faut aussi reconnaître les limites d’une telle pratique. La fabrication d’un véhicule passe par des opérations de grugeage des tubes afin de pouvoir en souder les jointures. On parle aussi de gueule de loup, lorsqu’il s’agit de gruger une extrémité. Les joints à souder doivent s’approcher de la perfection. Si de la matière dépasse, l’assemblage ne pourra pas se faire, les pièces ne rentreront pas l’une contre l’autre. Si on retire trop de matière, la soudure sera hasardeuse, il y aura effondrement du bain de fusion (on fait des trous) ou pire encore, il y aura une déformation thermique, avec des risques important de perte de symétrie du cadre. Il est possible de gruger à la main, avec une meuleuse, ou encore d’utiliser un outil prévu pour. On peut faire une grugeuse qui se contente de positionner une perceuse et sa scie cloche dans la bonne position et orientation par rapport à un tube. Je n’ai jamais utilisé cette outil, mais je doute de son efficacité sur des usinages en série, a fortiori si l’axe de la perceuse n’est pas concourant à l’axe du tube à découper, ce qui peut arriver.
Quand on s’interroge sur les possibilités d’usinage face à ce défi, on n’en vient forcément à découvrir le monde des CNC, et vouloir en savoir plus. J’ai rapidement décidé d’en faire une qui ferait de la découpe plasma. C’est moins contraignant en terme de rigidité de la machine, puisque la torche n’entre pas en contact avec la matière travaillée. Aucune force donc, ne contraignant la position relative de l’outil (la torche plasma) et la matière, si ce n’est un insignifiant flux d’air comprimé employé par ce procédé. C’est un aspect important quand on découpe des tubes, car pour ce faire on utilise un 4ème axe, outre les trois axes du plan cartésien de mouvement de la torche. Ce quatrième axe est celui de la rotation du tube ou profilé sur son propre axe. Il faut pour cela mouvoir le tube par le biais d’un mandrin, similaire à celui des tours à métaux. Le tube n’est tenu que par une extrémité si on découpe l’autre extrémité, et une contre-pointe est de toute façon d’un secours limité, avec la souplesse du tube à découper, la variabilité de sa longueur (et donc de la position de la contre-pointe) on ne peut pas réaliser facilement une opération de fraisage satisfaisante. Le plasma est en outre bien plus rapide. Le choix entre plasma et fraisage reste discutable, je pense que le fraisage reste faisable et serai ravi à l’avenir de disposer d’une machine pouvant le faire, mais c’est un défi difficile pour un usineur débutant. J’ai donc choisi la CNC plasma, avec un 4ème axe, c’est déjà assez complexe.
Après bcp de travail de fabrication et mise au point, voici un premier aperçu de que peut faire la machine. Les ajustements en vitesse de coupe permettront à terme des rebords encore plus nets et propres.
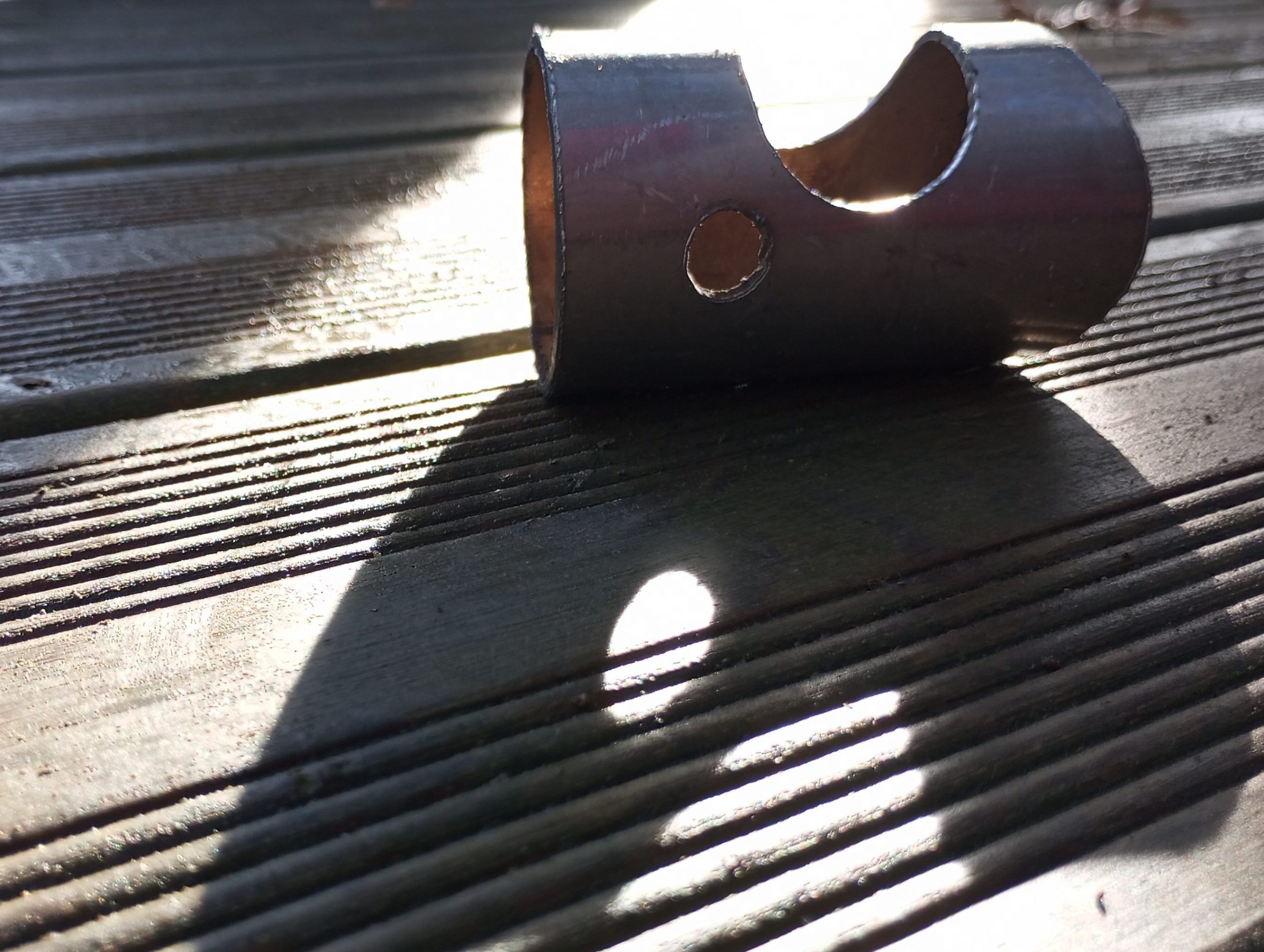
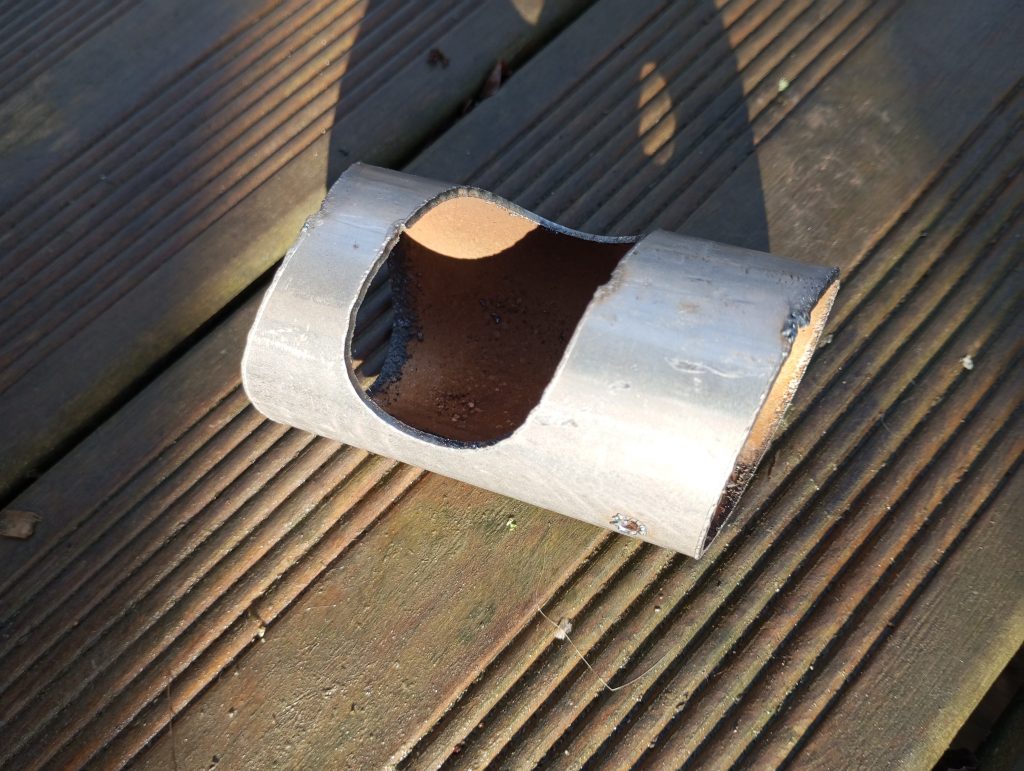
Mes choix de matériels, construction et logiciels
Pour les curieux ou personnes en recherches de références, je me suis basés sur les logiciels, architectures et matériels suivants :
Logiciels :
CAO : FreeCAD
FAO : SheetCAM & son plugin rotary axis
Firmware de la CNC : GrblHAL
MPU et Break-out Board : Teensy 4.1 et T41U5XBB de Phil Barrett ; stream par cable Ethernet (éviter arduino par USB si vous avez des interférences électromagnétiques)
Streamer et configuration software de la CNC : Io Sender (Terje Io est aussi le développeur derrière GrblHAL)
A envisager pour simulation : GrblGRU (voire même pour usage en streaming, mais seulement par port USB)
Géométrie/architecture de la machine : Le modèle de JD Garage à l’origine, trouvable sur Youtube. J’ai du le modifier depuis, beaucoup de défauts et de limite, beaucoup de travail et temps perdu. Les designers ne sont pas constructifs sur la possibilité d’améliorer, de contribuer. A posteriori, et pour différentes raisons, Pas cher à construire financièrement, mais JE NE RECOMMANDE PAS.
A privilégier ou étudier pour une CNC polyvalente à terme : modèle PrintNC avec adaptateur d’outil à concevoir pour y fixer torche plasma/broche de fraisage/laser.
Driver et élec de puissance:
Alim 36V
Drivers : TB6600 à éviter, trop fragile et DM556 = ok
Moteurs NEMA23, au minimum 3A et 2Nm, y compris pour l’axe Z
Connecteurs aviation GX16
Câbles blindés, bien dimensionner le diamètre selon longueur et courant
Générateur plasma :
-HC8000 de HeroCut, avec torche droite pour CNC, rallonge de torche 8m
-génrérateur ParkSide en appoint ou pour faire des tests, usage manuels aussi ; pas cher, HF émet des interférence électromagnétique
Imprimante 3D pour fabrication des pièces :
Ender 3 d’occasion, attention, requiert tout de même un peu d’apprentissage et de maintenance. Logiciel slicer : Prusa Slicer
Compétences requises
Une CNC coûte cher, surtout si on des besoins bien spécifiques, c’est souvent pour cela qu’on préfère la fabriquer soi-même. Mais l’auto-fabrication réserve bien des surprises, est largement plus chronophage que ce que l’on imagine. Fabriquer et exploiter une CNC repose sur des compétences variées :
-design et conception assisté par ordinateur ; avec le logiciel de son choix. J’encourage vivement FreeCAD, opensource et assez ergonomique depuis sa version 1.0, plein de fonctionnalités. Il s’agit d’une part de créer et fabriquer les pièces pour monter la CNC et s’assurer de sa bonne géométrie, d’autre part d’utiliser le logiciel pour dessiner les pièces à usiner
-impression 3D ; pour réaliser les pièces d’assemblage de la CNC quand on a pas de fraiseuse. De nombreuses pièces complexes sont requises, dans lesquelles insérer des roulements, vis, écrous, guide linéaires, fixer moteurs et poulies. L’impression 3D est aujourd’hui largement étudiée et sollicitée pour faire des CNC abordables. Les principaux défauts sont d’une part la faible résistance à la chaleur (surtout dans le cadre de la découpe plasma : pièces qui fondent ou se déforment, à réimprimer, il faut faire sinon des carters de protection en métal) et d’autre part la relative flexibilité (surtout pour le fraisage sur matériaux durs, qui requièrent une machine très rigide ; certains font d’abord une CNC en pièces imprimés, pour pouvoir ensuite usiner de l’aluminium afin de remplacer les dites pièces)
-mécanique : évidemment, il s’agit de faire des assemblages, juger de la tension des courroies, de la puissance des moteurs d’ajuster le jeu des roulements, percer et tarauder dans le métal sans casser les tarauds, dans le plastic sans l’arracher, de refaire ou améliorer des pièces après un deux crashes de machines, inévitables comme erreur de débutant, apporter une rigidité suffisante pour l’ensemble
-électronique ; on part la fleur au fusil, sans se douter de certains risques. Les interférences électromagnétiques sont un véritable cauchemar pour les débutants optimistes. Il faut adopter un ensemble de bonnes pratiques de compatibilité électromagnétiques dans la construction de sa CNC. Protéger l’électronique sensibles par un ensemble de moyens et limiter / contenir les sources d’interférences, au moyens de filtres RC, opto-coupleurs, mise à la masse des carters. C’est en particulier le cas en présence d’une torche plasma à amorçage haute fréquence, ou d’un variateur de vitesse (VFD) pour une fraiseuse ou un tour. Avant-même ces défis, il s’agit de savoir correctement souder différentes épaisseur de fil électrique, du PCB sans endommager les circuites intégrés minuscules à côté , de savoir dénuder, isoler et blinder proprement des soudures entre fils blindés, flasher une carte électronique, bien référencer les multitudes de fils pour s’y retrouver, s’approvisioner en matériel électronique exotique…
-des compétences plus générales en terme de créativité pour répondre à des problèmes inattendus, et d’analyse pour diagnostiquer les causes de ces problèmes, surtout quand les causes sont multiples ou peuvent l’être
-enfin une bonne dose de volonté, si ce n’est de l’acharnement, pour persévérer malgré tous les obstacles imprévus.
En résumé, un avis aux curieux : Les CNC ouvrent de nombreuses possibilités, en terme de travail de matériaux variés, avec une vitesse et une précision inégalable par le travail artisanal, mais leur usage repose sur des compétences variées, éventuellement longues à toutes acquérir. Il faut une sacré dose de patience, d’effort et d’optimisme si on veut en venir à bout. L »autre possibilité est celle d’acheter des machines toutes faites, on y gagne bcp de temps, au risques de se voir limité dans les usages qu’on peut en faire.
Mes projets de CNC à court et long terme :
Avec beaucoup de temps devant moi, je réaliserais un routeur du modèle PrintNC, qui peut se monter avec des pièces imprimées en polymères plastiques, puis à partir de cette première version refaire les pièces en fraisant dans aluminium, ce qui rendrait la machine capable de fraiser même de l’inox ! Je voudrais cependant qu’elle est ait la même surface de travail que ma machine actuelle, presque 2x1m, ce qui rend incertain ou plus complexe une telle performance. La rigidité et la performance d’une CNC, c’est tout un travail d’ingénierie.
J’aimerais également avoir un petit tour à commande numérique, dans l’idéal avec contrôle de la vitesse de broche pour pouvoir faire des filetages. Le tour est très utile en mécanique cycle, qui repose beaucoup sur des profilés ronds, des ajustements précis de diamètres et parfois des enmanchements en force.
Mais il s’agit d’avoir un sens des priorités. La construction et le réglage de machines, tout cela est instructif et puissant mais chronophage, autant d’investissements qui ne sont pas amortis rapidement. Dans un premier temps je serai content d’exploiter correctement ma machine :
-bien calibrer ma découpeuse plasma, selon différentes vitesses de coupe, taille de buse de torches, matériaux et intensité.
-poser le portique de l’axe »X » sur ses des deux côtés, jusque là il est en porte-à-faux, porté sur une seule extrémité par une navette « Y » sur un rail de guidage. Ce porte-à faux est problématique dès que la navette X s’éloigne de son origine et du rail de guidage déjà installé. Mon 4ème axe, l’axe rotatif, pour découpe de tubes et profilés, est proche du rail Y et donc de l’origine de X, donc pas de problème pour lui. Par contre la découpe de tôle est précaire pour le moment, même avec un « Torch Height Controler(THC), je parie, qui est encore à installer. Il s’agit donc d’installer un deuxième rail de guidage » Y’ « à l’autre extrémité du portique, de bien calibrer son parallélisme au premier rail Y, et bien calibrer son interrupteur de fin de course afin que les moteurs en miroirs assurent une bonne perpendicularité entre le portique qui sert de rail à l’axe X et ses deux supports servant de rail à l’axe Y .
-un système de levage pour suspendre la machine et la ranger en hauteur. Elle mesure plus de deux mètres par un, bientôt un peu plus avec le 2nd rail Y, autant dire que ça occupe de la place dans l’atelier, même quand je ne m’en sert pas.
-carters de protection des pièces imprimées contre la chaleur
-un système de support des tubes plus efficaces. Le mandrin du 4ème axe, l’axe « A », ne tient qu’une extrémité du tube à découper. Pour éviter le porte-à faux, la flexion du tube sous son propre poids, des roulements servant de support sont installés sur un « sabot » en plastic. Ce système est positionnée et déplaçables le long d’un rail installée sous le tube à découper. Les tubes ronds peuvent rouler directement sur les roulements, mais il faut que ces supports maintiennent le tube à découper dans l’axe A, autrement dit parallèle à l’axe Y. Pour différents diamètres, il faut donc ajuster la hauteur de des roulements. Et pour les profilés non ronds, les roulements maintiennent des pièces imprimés, des « disques » intermédiaires de supports. Elles sont circulaires sur leur rebord extérieure, et ont en leur centre un trou de la dimension du profilé souhaité, pour pénétrer les dits profils dans la pièce imprimés avec aucun jeu. Ce sont autant de pièces différentes à imprimer, et parfois un nécessaire ajustement de la hauteur des roulements qui les soutiennent, rien de très efficace donc. Outre la fusibilité des pièces imprimées si elles prennent trop de chaleur, ce système ne permet pas de changer rapidement de type de profilé à découper et limite la taille des profilés en entrant en collision potentielle avec la torche ou le porte-torche. Je ne vois pas de solutions miracle pour ce problème, seulement plusieurs ajustements, des entretoises et hauteur de roulements bien identifiées, et macros anti-collisions.